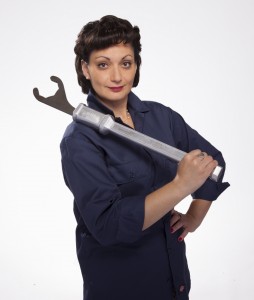
UW-Milwaukee Professor Naira Campbell-Kyureghyan designed a unique industrial wrench that reduces injuries among gas utility workers, prompting a Wisconsin-based tool company to snap up the license and sell the product.
The gas meters that measure energy consumption in buildings pose as great a threat to workers who service them as downed power lines do to electric utility workers. Left in place for decades, the meters are often painted over and rusted, making nuts difficult to budge. Heavy pipe wrenches can slip when workers apply excessive force, violently jolting shoulders and backs.
Nearly a third of injuries to gas utility workers come from changing meters using a traditional pipe wrench. Some of them, like torn rotator cuffs and quadriceps, require surgical treatment, costing thousands in medical bills and lost wages.
Determined to bring down the number of these injuries, Professor Naira Campbell-Kyureghyan and graduate students designed a tool that reduced the shoulder muscle activity needed for the task by 40 percent, while eliminating slippage. The researchers then sought input from Kenosha-based toolmaker Snap-on Inc.
“What I saw was a tool that improves the way technicians were doing their work,” said Andy Lobo, director of product management and development at Snap-on Industrial, a division of Snap-on Inc. Company officials liked the prototype so much that they licensed the idea and made some modifications of their own, which Campbell-Kyureghyan’s students tested in the lab and at utility companies.
Snap-on believes the wrench will be popular, and UWM stands to benefit from the company’s aggressive marketing strategy that targets public utility and power-generation customers.
Gas industry unites around safety
Campbell-Kyureghyan is devoted to using biomechanics to keep people safe and productive at work.
With a background in worker safety in the construction, energy and manufacturing sectors, she has studied a range of occupational hazards, including the effects of vibrations from
jackhammers, exposure to extreme heat, falls from ladders and even the effectiveness of protective gear, like boots and gloves.
After joining the UWM faculty in 2009, she discovered that little information existed on ergonomic conditions in the gas industry, so she formed the Consortium for Advanced Research in Gas Industries (CARGI), now an organization of more than 200 partner companies that pool resources to fund studies on various safety and productivity issues.
Forming CARGI stimulated more collaboration with industry, a priority at the College of Engineering & Applied Science. In their first year, CARGI partner companies decided it was time to search for solutions to the problem of wrenching injuries. Campbell-Kyureghyan’s students collected data on injuries that occur in the field, including thrown backs, torn arm muscles and over exertion, looking for the root causes in order to find solutions.
“Biomechanics is a very important part of tool design because you can’t see how the body is responding from the outside,” Campbell-Kyureghyan explained. “You need quantitative data on what’s going on the inside.”
Students researching the problem also identified solutions that weren’t working. Some gas technicians, for example, were lugging bags full of custom wrenches to and from job sites in an attempt to avoid injuries from slips. The additional tools raised the weight of the bags to between 50 and 80 pounds — enough to cause other kinds of strain.
The research also indicated that on-the-job injuries that occur repetitively constitute a substantial amount of the total health-care costs for companies, Campbell-Kyureghyan said.
It’s about people, not machines
Campbell-Kyureghyan came from an Armenian family of engineers. A talented student, she followed her parents into the engineering field, earning doctorates in both electrical engineering and biomechanics.
While completing her Ph.D. in biomechanics at the Ohio State University, she applied computational modeling to health care projects such as drug delivery for cancer treatment and musculoskeletal biomechanics.
“The work was so satisfying,” she said. “I realized I could use my engineering knowledge and apply it to people and their health rather than to robots.”
Inspired, she enrolled in medical school for a year just to learn the vocabulary necessary to collaborate with health professionals.
Campbell-Kyureghyan has spent the past decade continuing to model the effects of forces on the body, while completing four U.S. Department of Labor grants related to worker safety.
She developed that expertise as a faculty member at the University of Louisville, where her lab created research-based safety training materials for five different kinds of utilities. She and her
students toured the country for 18 weeks, documenting the worst threats to safety in each environment, looking for solutions and training those who trained the employees.
“We encountered horrible accidents, like electrocution and deaths caused by falling tools. The injuries we looked at were not incidental problems,” she said. “They were repetitive and chronic – and all preventable.”
Campbell-Kyureghyan’s wide range of expertise has made her a go-to source for policymakers. Last year, she was invited by the National Aeronautics and Space Administration to give a talk about her research on training to prevent job-related hearing loss. The Department of Labor has used her work to improve safety in foundries and small metal-casting businesses.
“She has a compassion for everyday workers and the risks they have to take to make the rest of us comfortable,” said Karen Cooper, a former research colleague who is now the safety manager at Nissan North America. “The guys who go out in a storm to restore power to people’s homes. The gas technician who works in all kinds of weather, but can even be hurt by something as simple as a wasp nest near the meter.”
A tool that unites a community
The new “ergo” wrench is just as rugged as a pipe wrench, but lighter with a longer handle and a head that fits securely to the nut, dramatically diminishing muscle activity in shoulders. The shape of the handle provides a more comfortable grip and reduces pressure points on the hands by 20 percent. A quick release mechanism allows for speedy swapping of four interchangeable heads, meaning technicians don’t have to carry multiple tools.
Lobo said collaboration with UWM researchers on the gas-meter wrench has laid a strong foundation for future partnership.
Along with academic researchers and private-sector engineers, about a dozen students worked on the project in the past three years.
The diversity of people uniting to solve a problem, including students and potential users of the product, is exciting to Andy Ginger, president of Snap-On Industrial. He believes it’s emblematic of American innovation.
“These kinds of projects are very important — matching ideas with the efforts of the many,” Ginger said at the 2015 product launch. “Matching universities and companies with the American people is the best weapon America has in winning in the global competition.”